Shaping the future of industrial motion
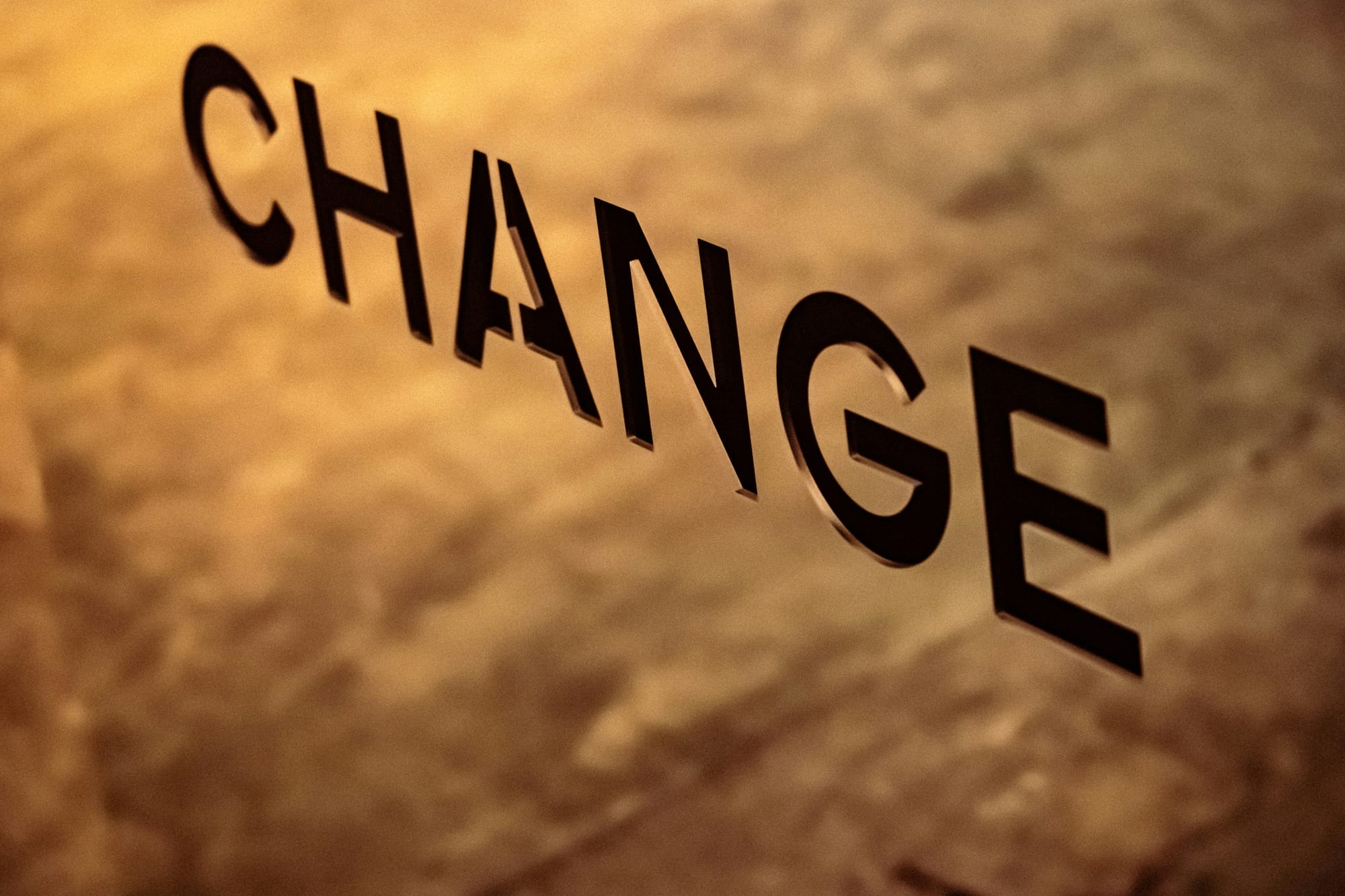
A virtual journey into the magnetic future
Join Damian for an exclusive, behind-the-scenes tour of LIRO technology where rotating shafts with permanent magnets promise to revolutionize motion in extreme industrial settings.
Arriving at Blackwater Industries
It was a bright morning when I first set foot in the sprawling complex of Blackwater Industries. Towers of piping and massive steel structures seemed to stretch for miles against the horizon. Beyond all the bustle of conventional mechanical systems lay a discreet, gray building marked with a small sign: LIRO Lab. That was my destination.
As I stepped inside, I met Damian, a tall, enthusiastic engineer whose eyes lit up when he saw me. "I’m so glad you’re here", he said, extending a friendly handshake. "We’ve been developing something extraordinary, and I can’t wait to show you". With that, he led me down a short hallway into a towering lab space, my curiosity growing with each step.
The LIRO lab revealed
The lab was far larger than I’d imagined airy, high-ceilinged, and dominated by an elaborate test rig in the center. A large, rotating shaft stood partially encased in a transparent housing, ringed by permanent magnets arranged at precise intervals. Next to it, a levitated platform hovered inside a rectangular metal frame.
Damian smiled at my wide-eyed reaction. "Meet LIRO Linear-Rotary technology", he said. "It’s similar in concept to a linear motor, except instead of long coils energized by electricity, we rely on phase-shifted permanent magnets spaced about 120 degrees apart on this rotating shaft. As the shaft spins, the magnets produce a "traveling" magnetic field that interacts with magnets on the platform".
I approached carefully, marveling at how the platform seemed to float, free of any mechanical contact.
How the traveling magnetic field works
"Watch this", Damian said. He pressed a button on a small control panel off to the side. A low, steady hum began as an external motor set the shaft spinning. The platform, previously motionless, started gliding smoothly along the frame, moving forward, then reversing direction. It was eerily silent no grinding gears, no squealing belts, just a gentle whir.
"Unlike standard motors that need continuous coils and lots of electrical power", Damian continued, "LIRO harnesses permanent magnets to generate propulsion and levitation. The rotating shaft is the heart of it all. The phased magnets create a magnetic wave that "pushes and pulls" the platform along no physical friction, no cables, no complex electromagnet arrays".
He chuckled at my stunned expression. "You’d be amazed at how little external energy we need. We only power a small motor to keep the shaft rotating. The rest? It’s pure magnetism at work".
A peek behind the magic
Damian guided me closer, inviting me to observe how the platform hovered. I leaned in, noticing the underside of the floating base another array of magnets that aligned with the spinning shaft’s field.
"The magnets on the platform and the shaft are carefully arranged so they repel and attract each other at just the right times", he explained. "They’re all set at 120-degree offsets, ensuring a smooth, continuous force. It’s basically a linear motor turned inside out except here, the magnets move, and we don’t need long electrical windings along the path".
I pressed my hand near the platform’s edge, sensing a faint buzzing as the field’s invisible waves rippled into the surrounding space. It was unlike anything I’d experienced powerful yet seemingly effortless.
Perfect for extreme environments
Damian led me toward several smaller prototypes arranged on benches around the lab, each labeled with names like "High-Heat Unit" and "Corrosion-Resistant Rig".
"When you rely on permanent magnets for levitation and propulsion", he said, "you’re free from a lot of the issues that plague conventional systems. No electrical coils to short-circuit, no friction to create heat or sparks, no oil-based lubrication to fail in harsh conditions".
He rattled off scenarios where LIRO would shine:
- Explosive Atmospheres in petrochemical plants, where a single spark can trigger disaster.
- High-Temperature furnaces or cryogenic environments that would destroy typical motors.
- Cleanrooms for pharmaceuticals or semiconductors, where contamination from lubricants or dust can ruin entire production lines.
- Nuclear Facilities, where electronics degrade under radiation, but permanent magnets don’t.
- Mining Operations, filled with dust and debris that clog conventional machinery.
"Every place you can’t normally use a standard motor LIRO can step in", Damian said. "The platform doesn’t rely on mechanical bearings or metal gears in contact, so there’s really nothing to corrode, jam, or spark".
Trials in the test chambers
We walked by several sealed glass enclosures designed to simulate extreme conditions. In the first enclosure, a high-heat oven, a LIRO prototype spun steadily at a scorching 400°C. Damian pointed out how the lack of electrical windings prevented anything from melting or shorting, highlighting the value of permanent-magnet operation in elevated temperatures.
In another enclosure, a cryogenic chamber, a second LIRO unit functioned below –150 °C, its shaft and magnets frosted yet unfazed by the cold. Damian explained that, in conventional systems, lubricants might freeze or electric coils could crack under such conditions, but LIRO’s permanent-magnet approach bypassed those pitfalls.
A steel platform in a corrosive-fog enclosure was the final stop. Immersed in harsh acidic vapors, the platform remained rust-free due to the use of stainless steel, Inconel, and specialized coatings. "It’s all about the materials", Damian said, tapping the chamber’s viewing window. "We pick corrosion-resistant metals and apply protective layers to the magnets. And with no motor coil to burn out or short, we can push LIRO further than conventional solutions".
Industry-wide applications
As we moved on, Damian directed my attention to diagrams illustrating how LIRO technology could integrate into various industrial processes. In the food and beverage sector, a levitated conveyor would simplify wash-down procedures, eliminate grease, and maintain hygienic standards. By removing mechanical contacts, LIRO could safely handle everything from raw produce to packaged goods.
In pharmaceutical and biotech settings, LIRO could transfer fragile vials without risking contamination. No friction or airborne particles would compromise sterility, making it ideal for cleanrooms and controlled labs.
For the petrochemical industry, the spark-free nature of permanent magnets would prove invaluable in explosive zones. LIRO systems could transport volatile liquids or gases without the ignition risks seen in traditional electric motors.
In semiconductor manufacturing, stringent cleanliness requirements often demand ultra-clean wafer handling and minimal vibration. LIRO’s contactless levitation would help maintain purity, reduce particle generation, and achieve precise motion.
The mining and extractive industries presented yet another opportunity. Heavy loads moving through dusty tunnels could benefit from a frictionless, jam-proof design that eliminates the gear seizures and potential sparks common in mechanical drives.
In nuclear facilities, LIRO’s immunity to high radiation levels offered clear advantages. Managing radioactive materials with magnet-based motion could minimize downtime and reduce the risk of electronic failures under intense radiation.
Military and defense also stood out as a promising arena. Damian explained how the absence of friction and reduced electromagnetic signatures could be valuable in naval applications, where stealth and corrosion resistance are critical. Saltwater environments, notoriously harsh on mechanical systems, wouldn’t pose the same threat to LIRO’s sealed magnets and non-contact design. Meanwhile, in aerospace, LIRO’s ability to function without lubricants or electric coils makes it ideal for vacuum conditions or extreme thermal swings both of which are common in orbital and deep-space missions. The prospect of reliable, spark-free systems on spacecraft, satellites, or high-altitude aircraft could open doors to new designs that traditional actuators simply can’t match.
He paused, letting me take in the breadth of potential. "Our big challenge", he said, "is to show these industries that permanent magnets and a spinning shaft can outperform the motors they’ve relied on for decades and do so safely under extreme conditions".
The path ahead
Damian ushered me back to the main rig, where the floating platform still glided smoothly around the frame. "We’re steadily moving from lab prototypes to real-world pilots", he explained. "We’re testing in harsh, active facilities mines, refineries, even some high-tech manufacturing plants".
When I asked about reliability, he shrugged. "We’ve done millions of cycles without any noticeable wear. With no mechanical contacts, maintenance is minimal. That means longer operational life and fewer shutdowns".
He gestured to an array of monitors displaying simulations of various shaft configurations. "We run Finite Element Analysis (FEA) to optimize magnet placement for each application. The goal is to fine-tune levitation, thrust, and stability especially in the most punishing settings".
Envisioning a new era
Stepping away from the rig, I couldn’t help but picture how LIRO might reshape the world of industrial motion. Imagine factories where friction, heat, and dust-related breakdowns are a thing of the past. Or nuclear sites where the risk of electrical failure vanishes. Or cleanrooms where zero oil contamination is guaranteed.
Damian walked me to the lab’s exit and handed me a small pamphlet full of schematics and test data. "We’re convinced this is the future", he said. "It won’t happen overnight, but the momentum is building. LIRO can do things no other system can. For industries operating at the edge of what’s possible, it’s exactly what they need".
I thanked him for the tour, stepping out into the bright sunlight, my head buzzing with the possibilities. In a world where extreme environments routinely foil traditional machinery, LIRO stood out as a beacon of innovation leveraging the power of permanent magnets to float, move, and thrive where most motors falter. If this technology can continue to prove itself, the age of frictionless, spark-free, ultra-reliable industrial systems may be closer than we think.