Potential of LIRO technology to replace linear motors in semiconductor wafer processing machines
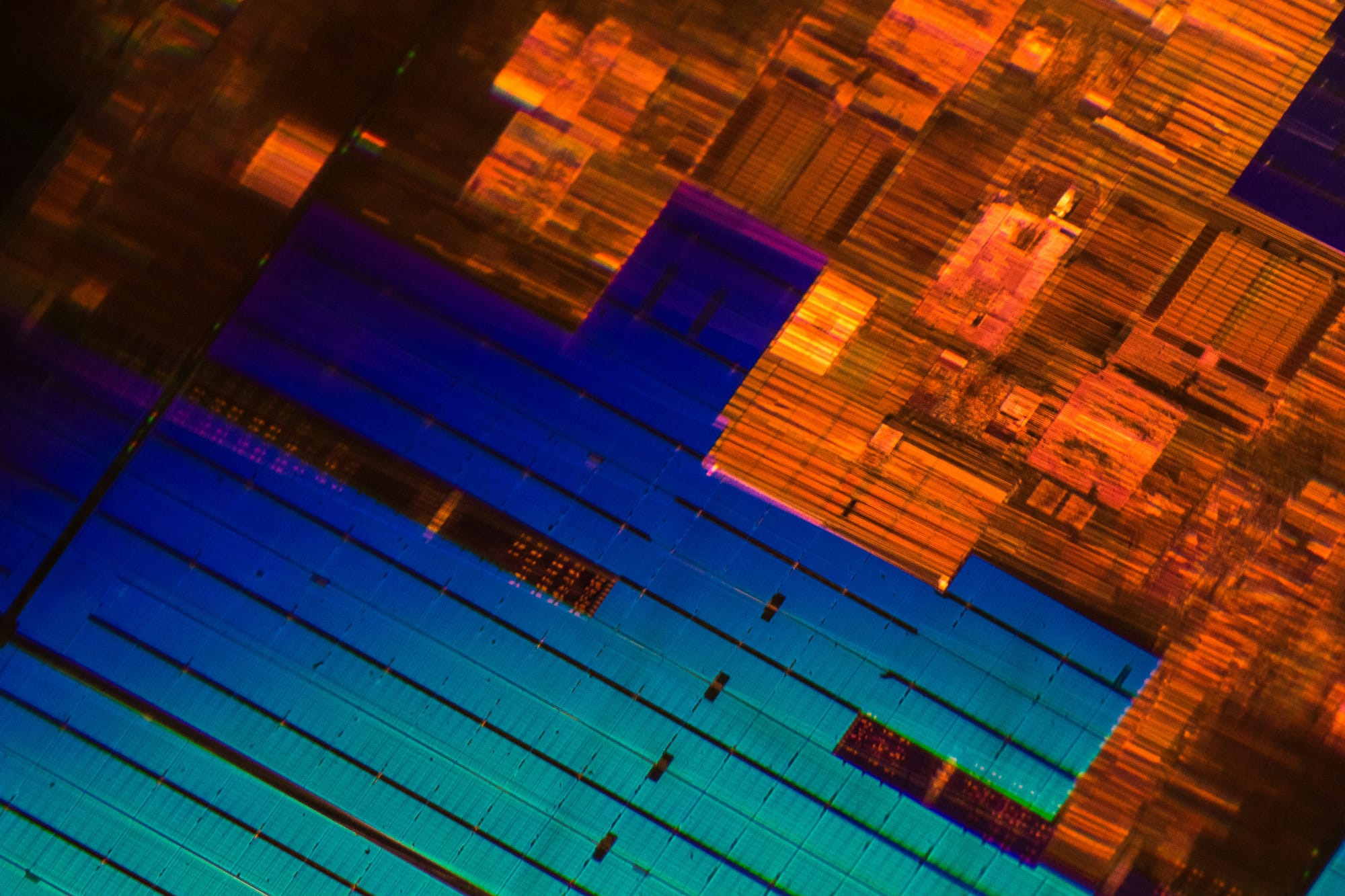
A new chapter in semiconductor manufacturing
Join Mihaela for a behind-the-scenes virtual tour of a high-tech semiconductor fab, where a groundbreaking motion system called LIRO promises to redefine wafer handling.
It was early morning when I first stepped into what seemed like the heart of tomorrow a vast semiconductor fabrication plant, or "fab", buzzing with a symphony of whirring machines and dancing robotic arms. For a moment, the hum of technology took on a pulse-like beat. Every corner promised something extraordinary. In this place, where the world’s smallest transistors are etched onto thin silicon wafers, even a single speck of dust is a major threat. Everything here is about precision and cleanliness right down to the specialized "bunny suits" worn by the engineers and technicians.
My guide for the day, Mihaela, was a senior engineer who had witnessed the industry’s evolution from the mid-1990s, when building a fab cost around €1.5 billion, to today’s cutting-edge facilities nearing €20 billion or more. "Back in the day", she said, leading me through immaculate halls, "we relied on linear motors and stepper motor actuators for nearly all wafer handling. They’ve served us well, but big changes are coming".
A glimpse into cutting-edge motion systems
In each step of wafer processing photolithography, deposition, etching, cleaning micro-meter or even nanometer precision is crucial. Over the years, linear motors have reigned supreme. They guide wafers through each production stage, providing stable, accurate movement that’s vital for maintaining yield. But these systems have drawbacks: moving mechanical parts wear out, requiring frequent maintenance, and they constantly consume energy to generate electromagnetic fields. Not to mention, they come with the risk of vibration and contamination, even in carefully controlled environments.
Then Mihaela told me about LIRO, a new technology that’s sparking enthusiasm not just in her fab, but across the industry. "LIRO", she explained, "is short for a rotary-linear motion system that uses magnetic levitation to solve some of our biggest challenges".
"In essence", Mihaela said, "we’re generating motion without the energy loss and mechanical wear you’d see in linear motors. LIRO uses permanent magnets to create continuous movement, so it draws minimal power and needs minimal maintenance".
A journey through the FAB with LIRO
To see how LIRO might reshape semiconductor manufacturing, we ventured deeper into the fab, tracing the path of a wafer from start to finish.
- Photolithography
- In a standard fab, wafer positioning under the intense UV light source demands nanometer-level accuracy, any misalignment can ruin entire batches. LIRO’s magnetic levitation offers ultra-smooth, contact-free movement, reducing the chance of vibration or wobble that might compromise the delicate photolithography patterns.
- Deposition
- From advanced systems like Chemical Vapor Deposition (CVD) to Atomic Layer Deposition (ALD), wafers spend time in vacuum chambers getting microscopic layers of material added. The gentler and more controlled the wafer’s path, the lower the contamination risk. LIRO’s modular design adapts to horizontal or vertical motion, giving engineers the freedom to optimize chamber layouts.
- Etching
- Etching requires precise, repeated transitions between plasma chambers. Here, too, non-contact motion keeps the wafer’s surface pristine. With LIRO, there’s less mechanical friction and no chance of stray particles from worn-out motor components.
- Cleaning
- In the cleanroom, maintaining a contamination-free environment is paramount. LIRO’s levitated movement helps prevent scratching or accidental contact that could degrade the wafer. It’s a perfect fit for processes where even the tiniest speck of debris can be catastrophic.
Throughout each of these steps, I noticed how quickly and quietly LIRO operated. Traditional linear motors can produce subtle vibrations, barely noticeable to the human ear but potentially significant at a nanometer scale. By removing direct mechanical contact, LIRO essentially eliminates a major source of unwanted noise.
Financial high stakes and future potential
As we passed another sealed chamber, Mihaela pointed out a sign listing the fab’s construction costs: €15 billion. It reminded me that building a modern fab is one of the most capital-intensive projects on Earth, a figure that can skyrocket to €28 billion for a 2nm-capable facility. Advanced equipment like Extreme Ultraviolet (EUV) lithography machines can cost up to €350 million each, and constructing the cleanroom alone can run around €1 million per square meter.
"This is why we can’t afford downtime," Mihaela said. "Every minute a machine isn’t running, we’re losing revenue that’s needed to recoup this huge investment".
With fewer maintenance interruptions, LIRO technology could help maximize operational efficiency. Beyond that, it could lead to energy savings, since the system relies on permanent magnets rather than constant power-hungry electromagnetic fields.
The global semiconductor industry is expected to grow by 6–8% annually through 2030, reaching around €1 trillion in revenue. Coupled with emerging trends like AI integration, advanced packaging, 3D printing, and quantum computing components, there’s a massive push to innovate on every front—including motion control. Some companies have already invested billions in new fabs tailored to produce high-speed AI chips. For them, LIRO’s potential is not just an engineering curiosity, it’s a strategic advantage for future growth.
Challenges on the road to adoption
No new technology goes mainstream without facing a few hurdles. For fabs that have relied on linear motors for decades, adopting LIRO might require:
- Retrofitting existing equipment: Integrating LIRO into legacy systems could demand custom parts and software adjustments.
- Initial investment: While LIRO promises cost savings down the road, the upfront expense of specialized components can be steep.
- Skilled workforce: Engineers and technicians must be trained to understand LIRO’s unique mechanics, magnet configurations, and troubleshooting procedures.
Yet these challenges mirror those encountered whenever a disruptive innovation arrives. Given the enormous long-term benefits, improved yield, reduced downtime, lower energy consumption, the semiconductor industry has proven it’s ready to invest when the payoff is compelling.
A glimpse of what’s next
On our way out of the fab, Mihaela led me to a corridor lined with posters detailing various pilot projects. One displayed a concept design for a next-generation production line powered solely by LIRO-based transport mechanisms. Another highlighted the synergy between AI-driven process controls and contact-free wafer handling, suggesting that these two innovations together could redefine productivity in fabs worldwide.
"We’ve reached a turning point", Mihaela concluded. "Where linear motors were once the undisputed champions, LIRO might become the new gold standard, especially as chipmaking gets more complex. The future of semiconductor production isn’t about small upgrades; it’s about transformative ideas. And I believe LIRO could be one of them".
I left the facility with a sense of awe and anticipation. In a realm where billions of euros and decades of research collide, the emergence of a new motion technology like LIRO isn’t just another technical curiosity, it’s a story of progress, ambition, and the relentless pursuit of perfection. If LIRO manages to deliver on its promise, the next chapter of semiconductor manufacturing might be levitated right before our eyes, propelling us into a world where technology can reach even greater heights, one contact-free wafer at a time.