LIRO artificial lift: The superiority of LIRO technology over existing artificial lift systems
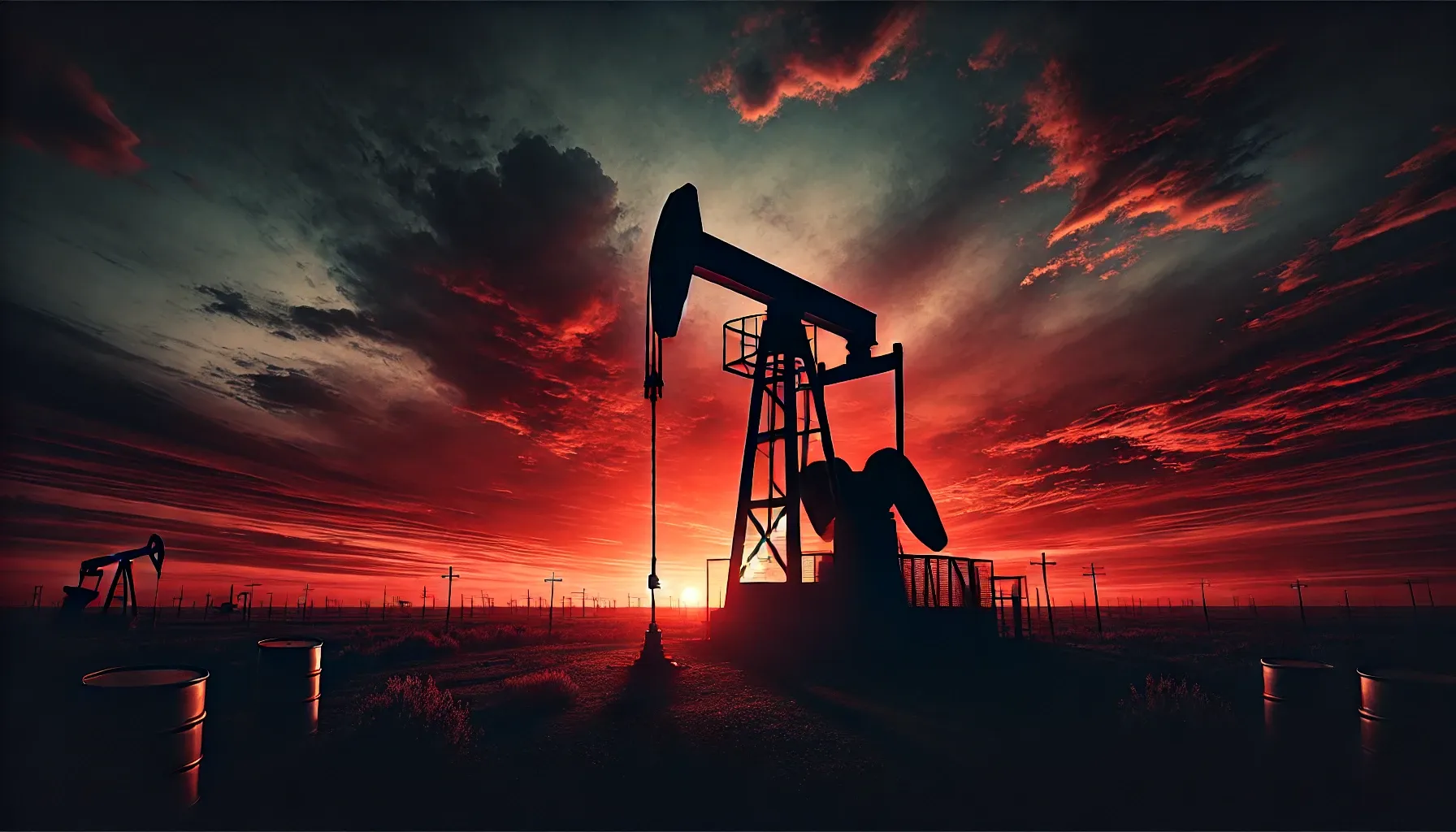
A new chapter in artificial lift: The story of LIRO
Join Nicolae for a behind-the-scenes virtual tour of a remote oil field, where a groundbreaking motion system called LIRO promises to redefine artificial lift.
A journey into the heart of Oil Country
It was well past dawn when our small plane landed on a dusty airstrip in a sprawling oil region, an industrial labyrinth of pumping units, drilling rigs, and endless rows of pipelines. My guide for the day was Nicolae, a veteran petroleum engineer with silver hair tucked under a hard hat.
Walking me through the hectic scene, Nicolae pointed to a row of nodding "horsehead" pumps: rod pumps, one of the most iconic sights in onshore oil fields. "These babies have been around for ages", he remarked. "They’re reliable but come with their share of headaches: mechanical wear, constant maintenance, and big energy bills".
He gestured toward a different area, where Electric Submersible Pumps (ESPs) were in operation. "They’re great for high flow rates," he said, "but imagine having to pull one out every time a part breaks, especially if you’re two kilometers beneath the ocean floor".
It was clear the traditional artificial lift toolbox, rod pumps, gas lifts, ESPs, and other methods, had propelled the industry forward for decades but wasn’t without challenges. Mechanical friction, routine repairs, and spiraling energy costs all meant downtime and lost revenue.
"But the industry is changing," Nicolae said. "Let me show you something new: LIRO".
Enter LIRO: A magnetic levitation marvel
After a short drive across the lease, we arrived at a newly installed pilot facility. Tucked away in a compact enclosure, it didn’t look like any pump system I’d seen before: no horsehead, no lengthy rods, just a sleek metallic shaft equipped with guide rails and magnets.
Nicolae explained how LIRO (Linear Rotary) technology works. At its core is a rotatable shaft lined with permanent driving magnets, each carefully spaced and phase-shifted. Attached to the movable element, responsible for transporting the oil-laden fluids, is another set of propulsion magnets.
When the shaft rotates, the phase-shifted magnets create a progressive magnetic field that levitates and propels the movable element. This motion can be configured for either vertical or horizontal transport of fluids. The genius? It’s contact-free, eliminating much of the friction and mechanical stress traditional pumps face.
"It’s like a maglev train", Nicolae said with a grin. "Except it’s for oil".
Why LIRO outshines conventional systems
-
Energy efficiency
In a world where upstream capital expenditures passed €600 billion in 2024, cutting operational costs is paramount. Traditional systems like ESPs and rod pumps continually gobble up electricity, largely due to friction and constant power-hungry electromagnetic fields. LIRO relies on permanent magnets, massively reducing power usage because it doesn’t depend on external energy to generate its magnetic fields. -
Reduced mechanical wear
With rod pumps, you have metal rods and plungers in perpetual motion, inevitably wearing down. ESPs have dozens of stages of impellers and motors, which must endure punishing conditions. LIRO’s frictionless design practically eliminates direct mechanical contact, slashing wear-and-tear and extending the time between interventions. -
Lower maintenance and operational costs
Downtime can cripple profitability, especially considering the global oil and gas sector’s revenues soared to €4.2 trillion in 2024. Every hour of inactivity is revenue lost. By removing most mechanical contact points, LIRO spares operators the grueling cycle of constant repairs and replacements, translating to fewer shutdowns and better bottom lines. -
Precision and control
LIRO systems excel at micro-adjustments, operators can tweak the speed, torque, or even the stroke length with near-instant responsiveness. In advanced extraction zones where reservoir pressure is unpredictable, fine-tuning the flow rate can help optimize production without overstressing the well. -
Versatility for varied conditions
Oil fields are as diverse as the planet’s geology: some have heavy, viscous crude; others contain high volumes of gas. LIRO adapts to these changing conditions. Whether pulling fluid from deep offshore wells or transferring oil horizontally in onshore facilities, the platform’s modular design and levitating motion make it a potential game-changer across different extraction environments.
Deep beneath the surface: LIRO in action
Nicolae led me to a control room, where monitors displayed real-time data from the new LIRO unit. Pressure readings, flow rates, and equipment diagnostics streamed in seamlessly.
"In the past," he explained, "we’d rely on rods or submersible pumps. If something jammed, we’d have to shut everything down, pull out the assembly, and fix it". He tapped a screen showing LIRO’s performance. "Now, we just keep going, non-contact means fewer snags".
As we delved into the system’s data, it was hard not to connect the dots with broader industry trends. The digital transformation of oil extraction is already here: from remote sensors monitoring well integrity to AI that optimizes drilling sites. Now, cutting-edge motion tech like LIRO fits right in, offering synergy between advanced analytics and the physically robust hardware that lifts our most critical resources.
Financial and technological context
The timing for LIRO’s arrival couldn’t be better. After years of price volatility, the oil market in 2024 is relatively stable due to excess supply and shifting demand, especially in Asia. While that stability provides a boon for new investments, it also demands cost-effective and energy-efficient solutions.
Analysts predict that oil prices could swing below €50 per barrel by 2025, driven by factors like rising U.S. production and economic softening in key regions. To stay profitable in that environment, operators need to maximize production while minimizing costs and downtime.
"It’s no wonder the industry is focusing on new technologies", Nicolae noted. "Every euro counts. LIRO might just be the edge we need".
Looking ahead: LIRO and the future of oil extraction
As the day wound down, we found ourselves standing on a metal platform overlooking rows of pumping units stretching to the horizon. The thought that a magnetic levitation system, something straight out of a futuristic sci-fi novel, could soon replace these century-old giants felt both exhilarating and inevitable.
LIRO isn’t just another incremental upgrade: it’s a promise of smoother operations, lower overhead, and more precise control at a time when efficiency is king. While early adopters may face challenges retrofitting this new tech into existing infrastructures, the long-term gains, fewer breakdowns, reduced energy consumption, and simpler maintenance, are hard to ignore.
A glimpse of what’s next
With the world of oil extraction rapidly evolving, embracing AI-driven insights, digital twins, and now high-tech motion systems, LIRO stands at the cusp of a transformation. It’s a shift that could reshape how we think about artificial lift, paving the way for a new generation of cleaner, more efficient, and more profitable oil production.
Nicolae leaned against the railing, gazing at the horizon where the late afternoon sun painted the desert in gold. "We’re always pushing the limits, drilling deeper, operating longer. LIRO’s a sign we’re not done innovating", he said. "If we can tap into this frictionless approach, there’s no telling how far we can go. In the world of oil, standing still is never an option".
I could almost feel the gears turning in the wider industry, a collective realization that, in the relentless pursuit of efficiency and profitability, the story of artificial lift was ready for a bold new chapter. And if the success of LIRO continues, we might look back one day and wonder how we ever managed without it.