A closer look at LIRO: How rotating magnets enable frictionless transport
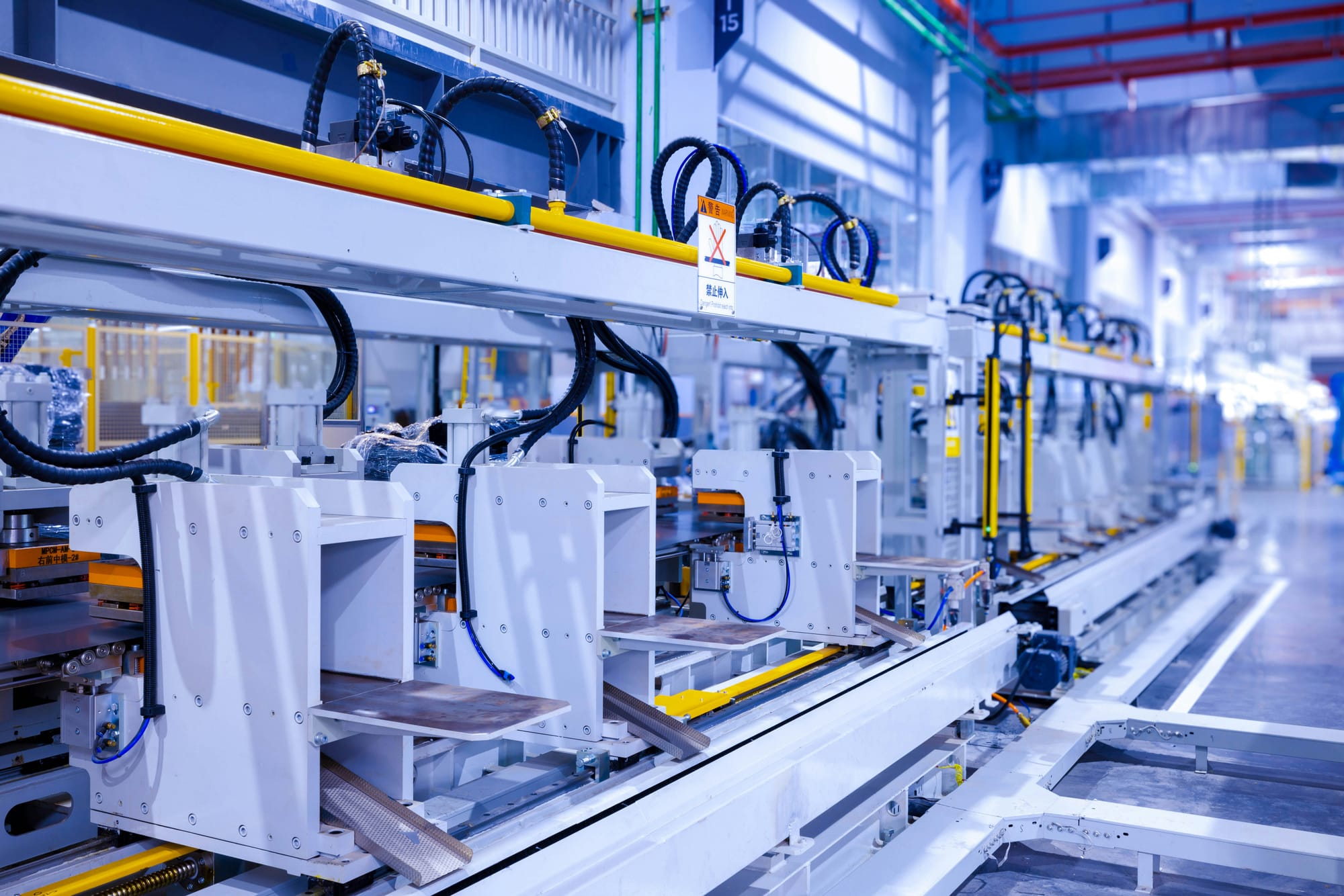
Picture a warehouse floor or a remote oil field where running electrical cables for a linear motor would be prohibitively expensive or simply impossible. Now imagine a system that achieves the same precise, frictionless motion but relies solely on the clever arrangement of permanent magnets. That system is LIRO (Linear-Rotational), and here is how it works.
The heart of the system: A rotating shaft with ring magnets
At the core of LIRO lies a rotating shaft. Around this shaft, ring-shaped permanent magnets are placed in a row, each rotated by ±120 degrees relative to the previous one. When the shaft spins, these magnets recreate the magnetic fields of a three-phase linear motor, only without the need for electromagnets or a constant power supply. The rotation of the shaft is provided by a small motor (which can be powered by any suitable means, from a simple motor to a hand crank in certain setups), but it does not require an ongoing electrical current to generate the actual lifting or propulsion forces. All of that work is carried out by the permanent magnets themselves.
Mathematical model of the magnetic field
The arrangement of ring magnets on the rotating shaft generates a magnetic field that behaves like a traveling wave, mimicking the effect of a traditional linear motor. Along the direction of motion (which we’ll define as the z-axis), this field can be mathematically described as:
$$ B(z, t) = B_0 \sin\left( \frac{2\pi z}{\lambda} - \omega_s t \right) $$
Where:
- \( B_0 \): peak field strength,
- \( \lambda \): wavelength, with d as magnet spacing,
- \( \omega_s \) : shaft’s angular speed,
- \( z \): position,
- \( t \): time.
This equation represents a magnetic field that moves along the z-axis at a speed of:
$$ \ v_s = \frac{\omega_s \lambda}{2\pi} \ $$
This speed, known as the synchronous speed, determines how fast the platform can move in sync with the field.
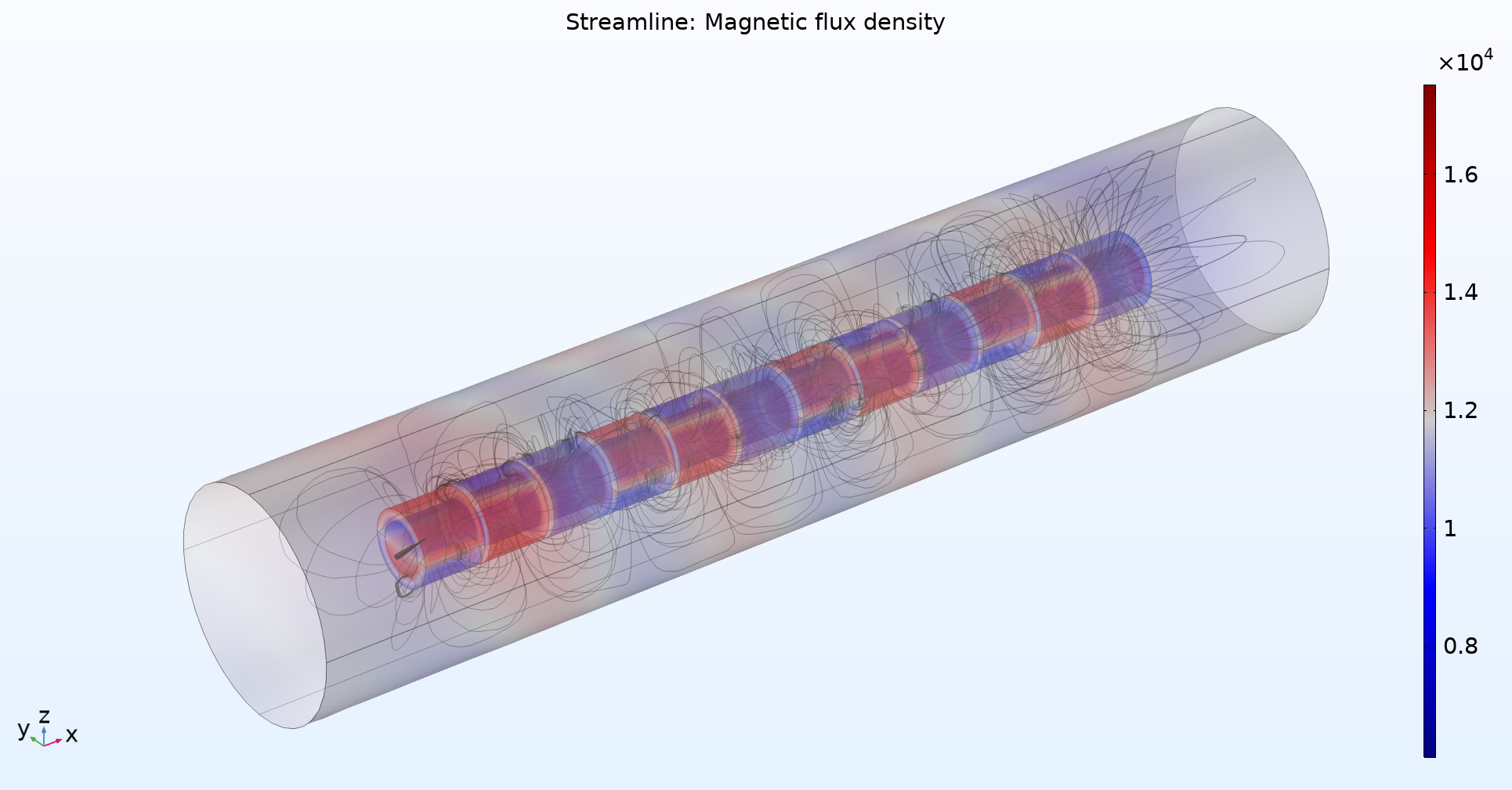
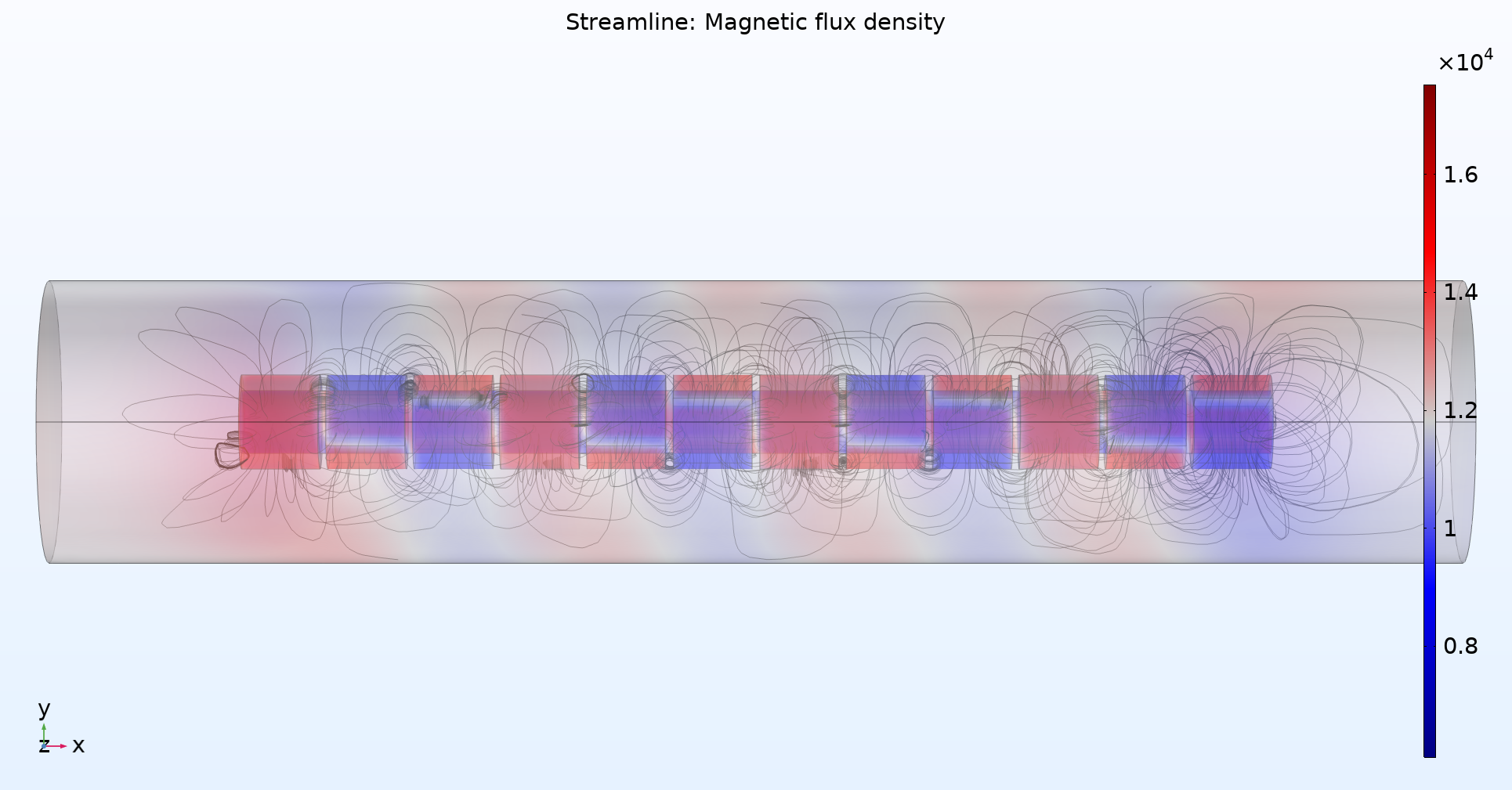
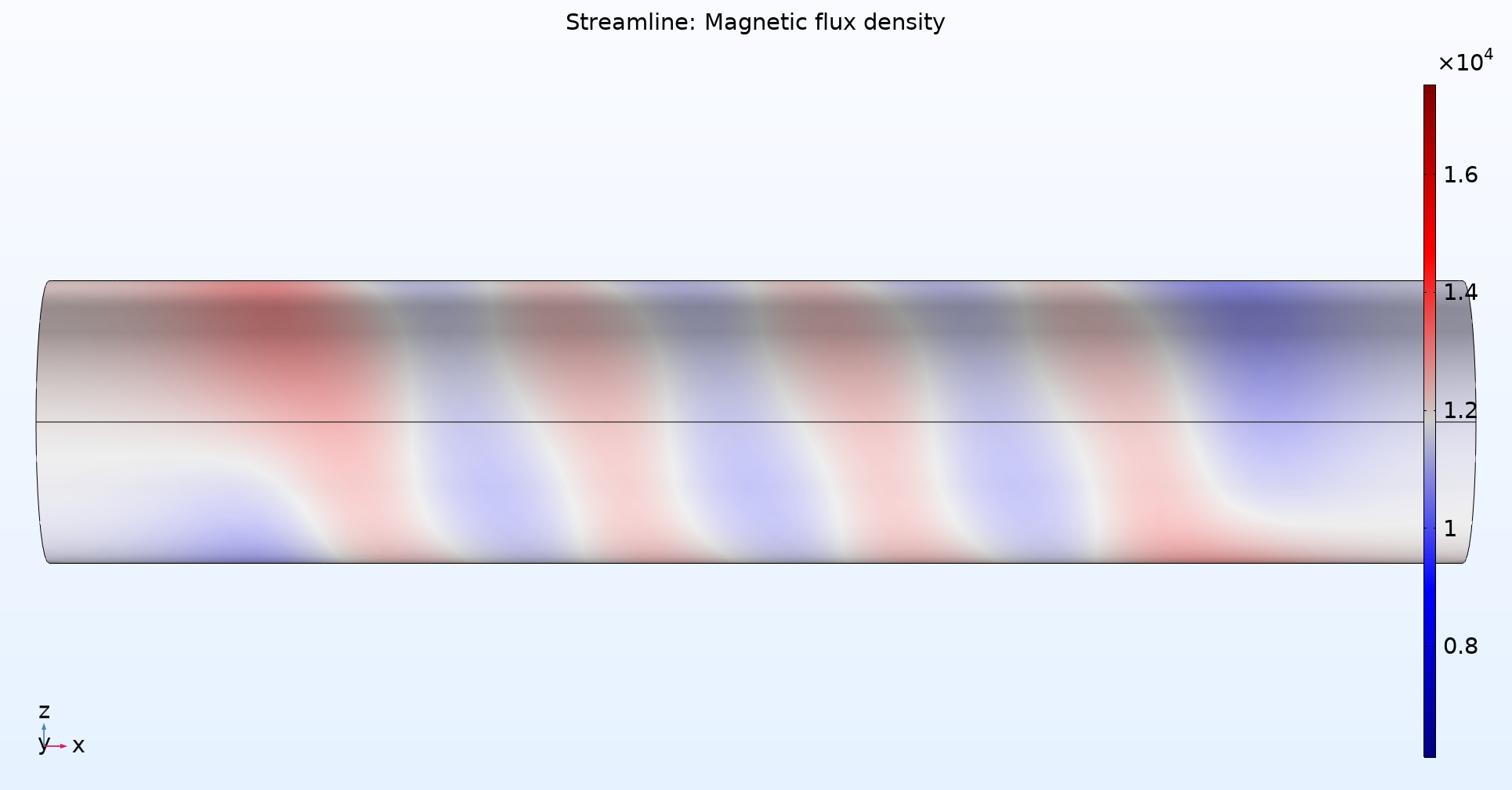
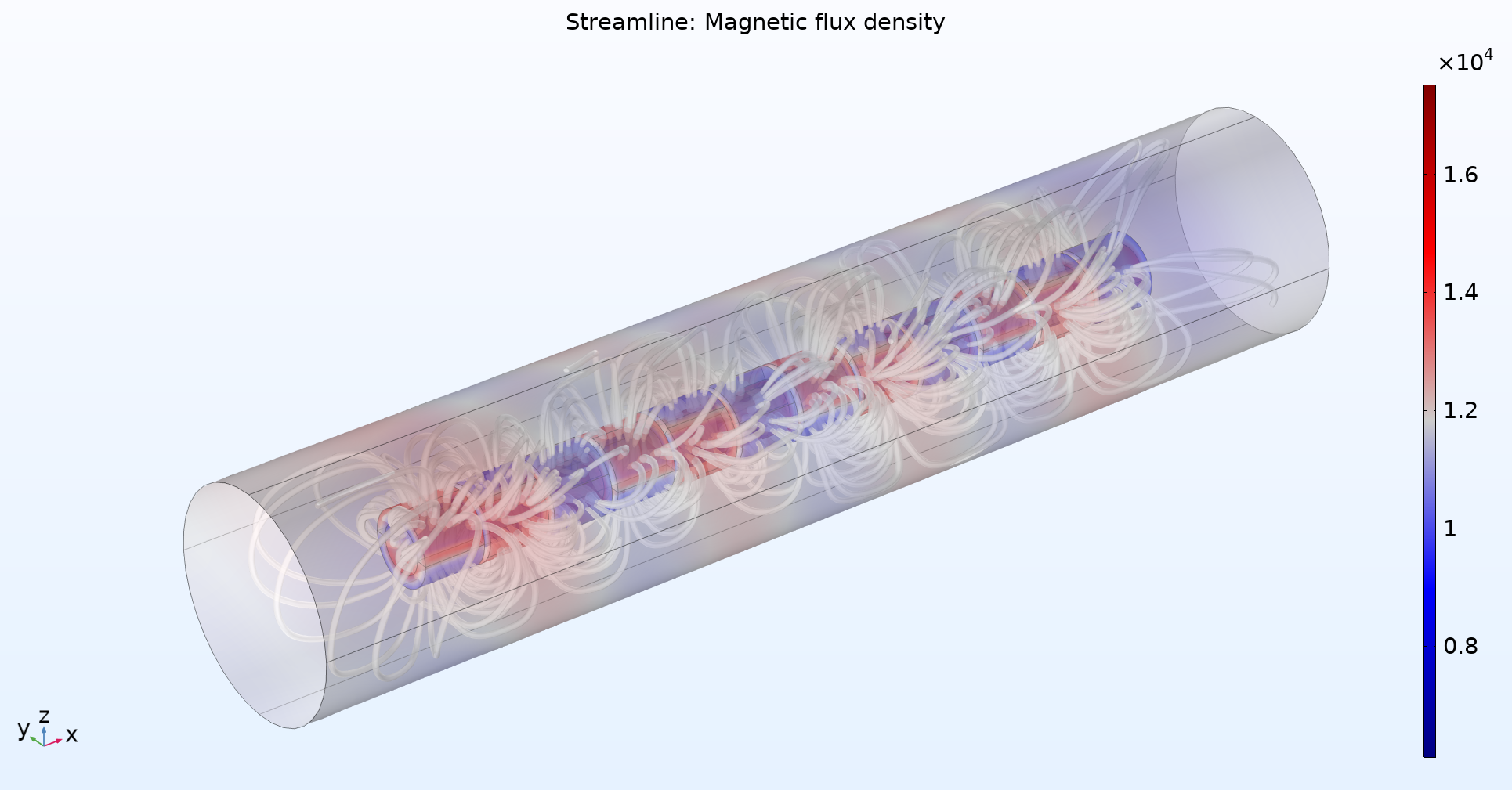
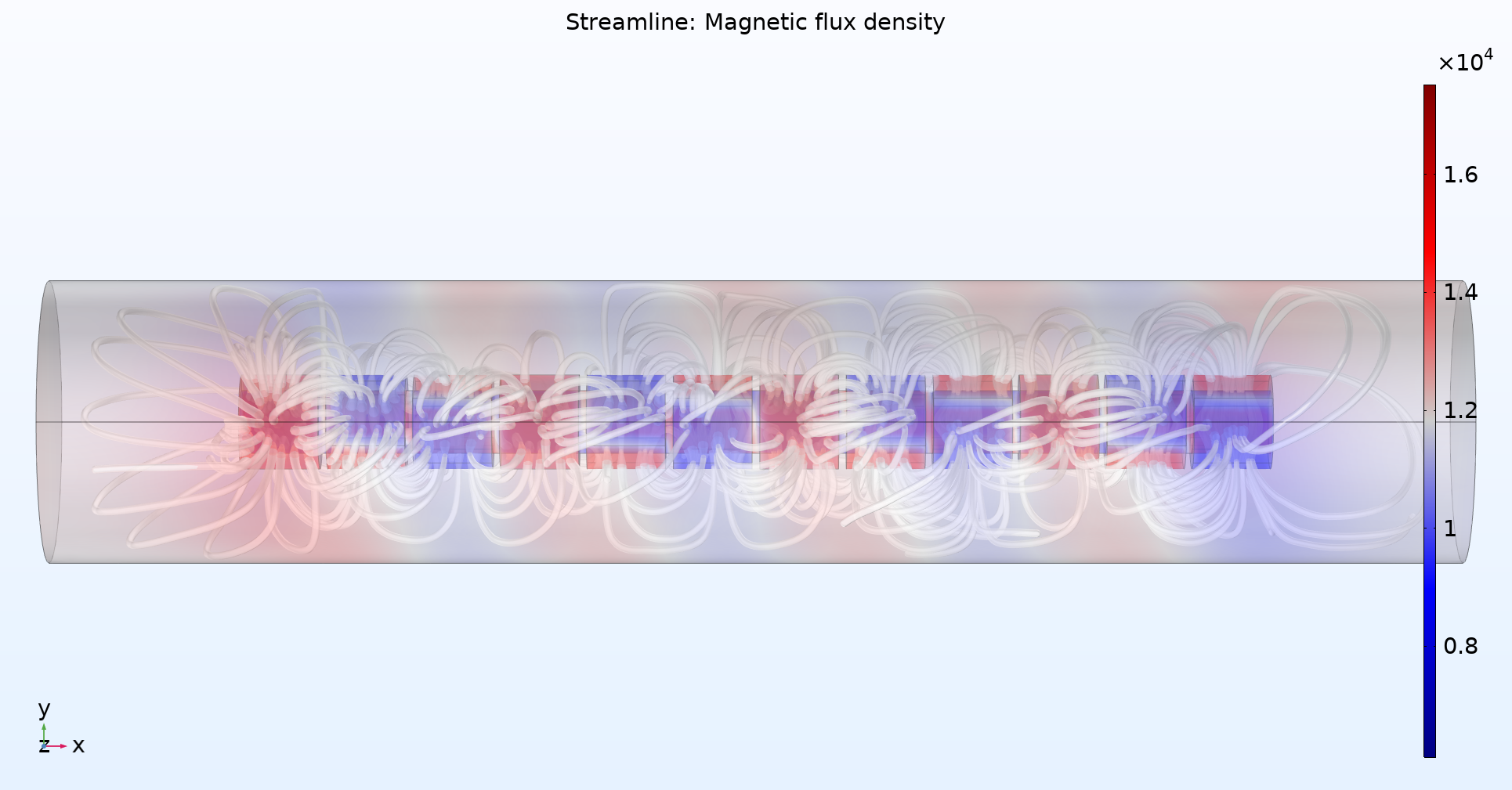
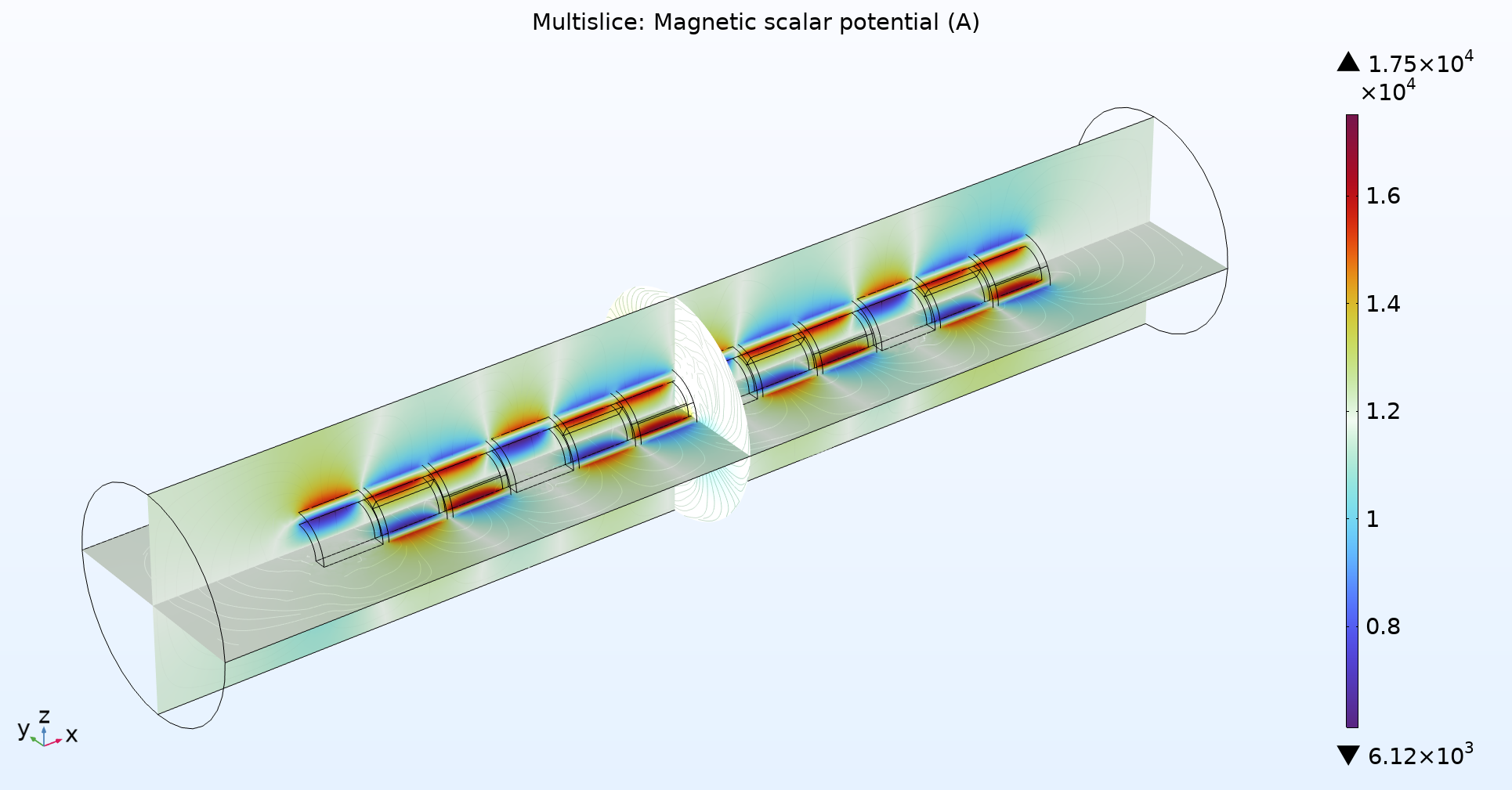
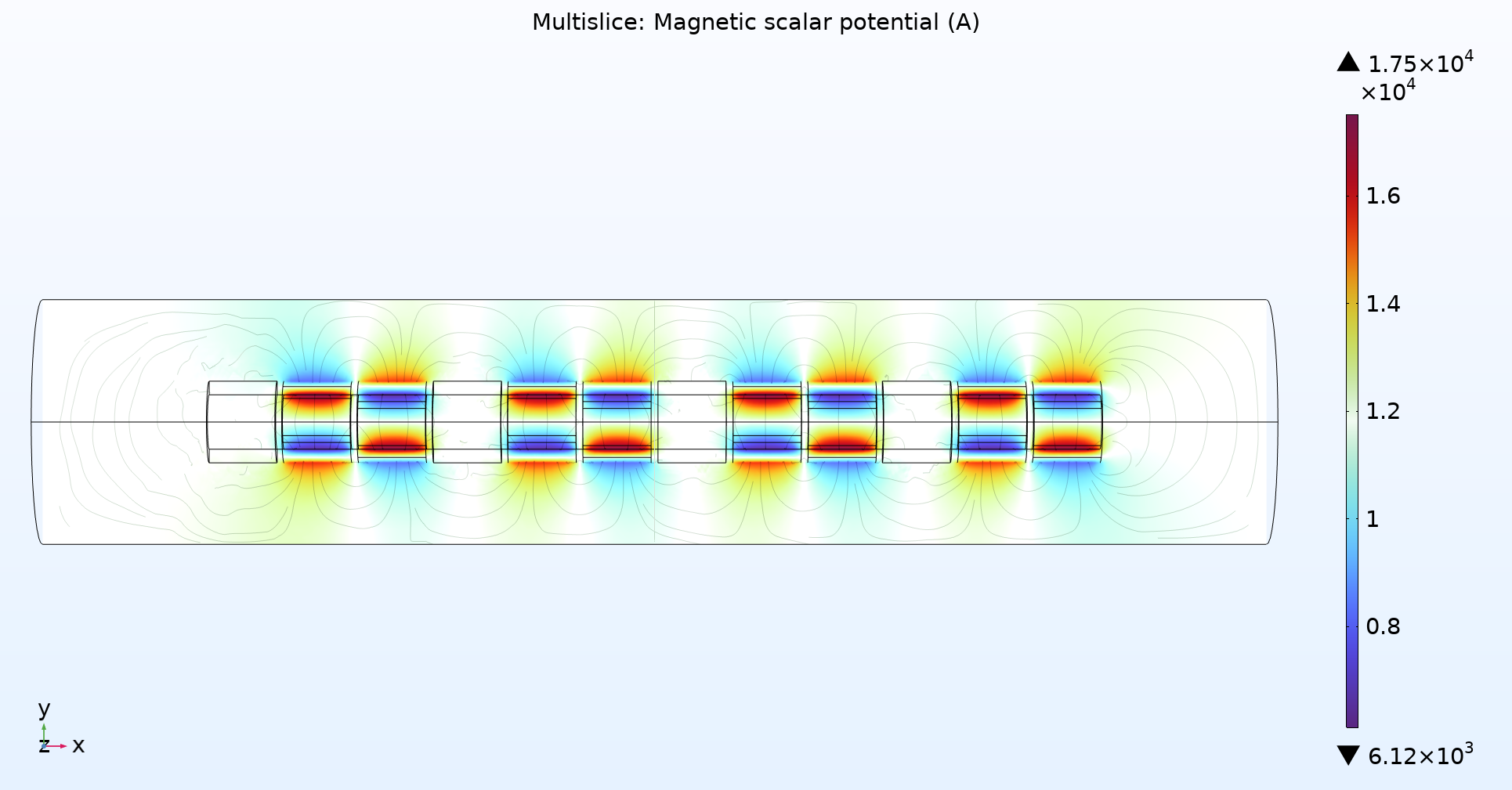
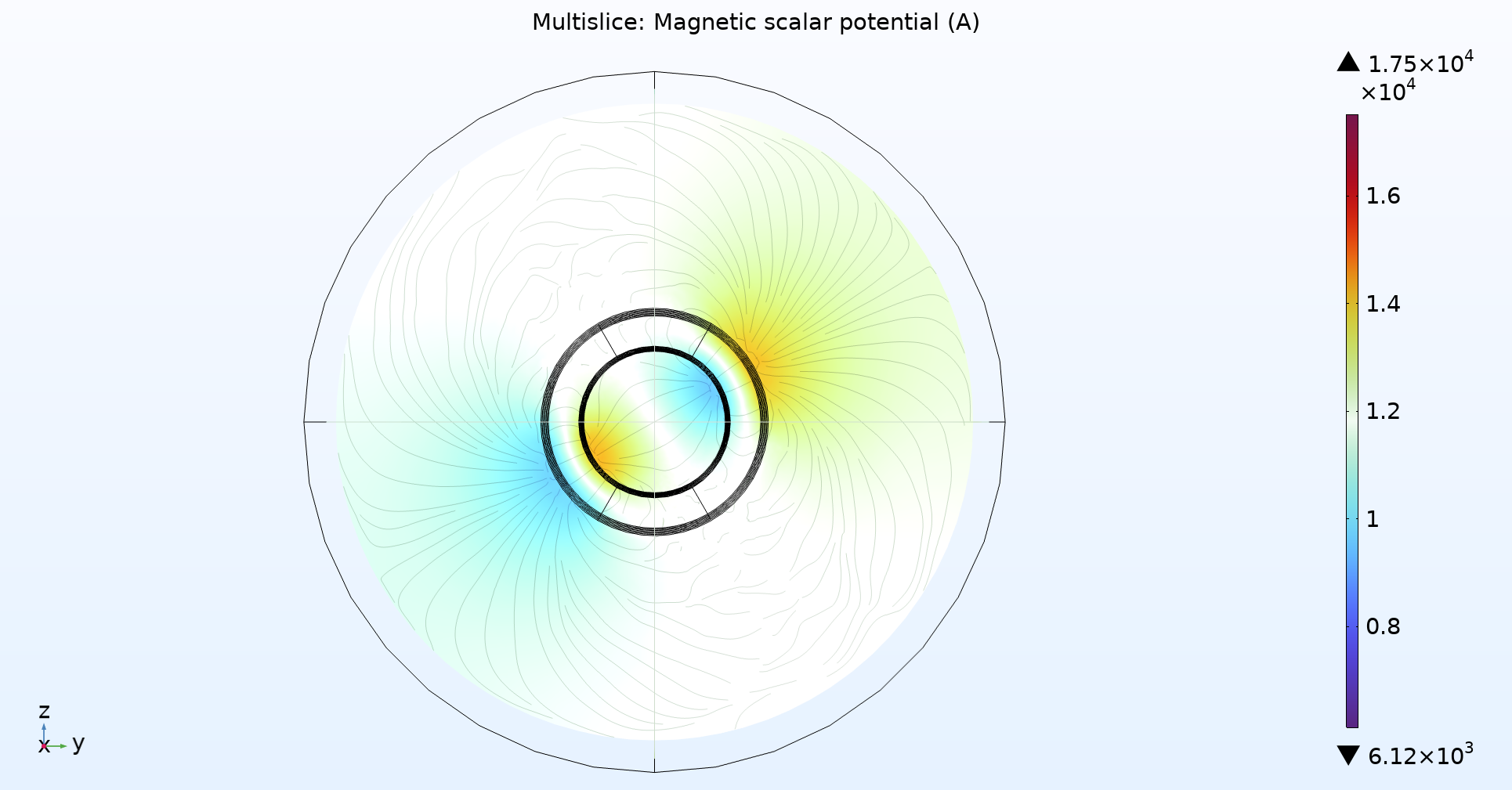
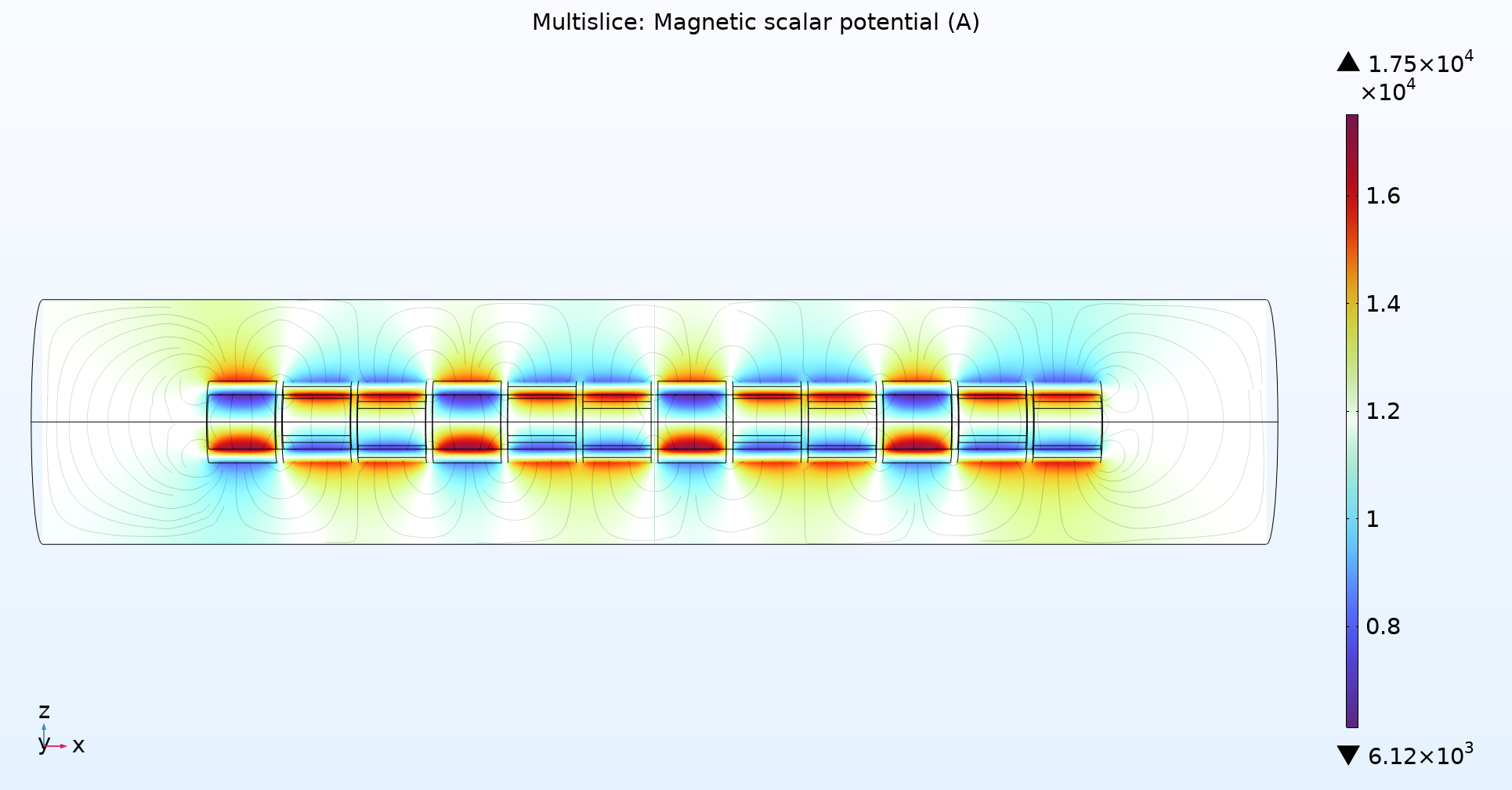
Magnetic fields on rotating shaft
Propulsion magnets on the movable platform
Directly interacting with the rotating shaft’s magnetic field is a movable platform equipped with its own set of propulsion magnets. These magnets are strategically positioned to engage with the traveling magnetic field produced by the ring-shaped magnets on the shaft. As the shaft rotates, the shifting poles of its ring magnets "push" and "pull" the platform’s magnets, resulting in linear motion that can be finely controlled simply by adjusting the shaft’s rotational speed. Because there is no physical contact and therefore no friction, this motion is remarkably smooth and quiet.
Force on the movable platform
The linear motion of the platform is driven by the forces between its magnets and the shaft’s traveling magnetic field. For a single magnet on the platform with a magnetic moment m, the force along the z-axis is given by:
$$ F_z = m \frac{\partial B_z}{\partial z} = m B_0 \frac{2\pi}{\lambda} \cos \left( \frac{2\pi z_p}{\lambda} - \omega_s t \right) $$
where \( z_p \) is the platform’s position along the z-axis. Since the platform typically has multiple magnets arranged to match the field’s pattern, the total force becomes:
$$ F = F_{\text{max}} \sin \left( \frac{2\pi z_p}{\lambda} - \omega_s t \right) $$
Here, \( F_{\text{max}} \) is the maximum force, which depends on the number of magnets, their strength, and the field’s properties. This force propels the platform, keeping it synchronized with the traveling wave when the system is balanced.
Magnetic rails for support and guidance
To ensure that the platform remains stable, LIRO employs two parallel rails. Along the edges of the platform, additional permanent magnets are mounted in such a way that they constantly repel similar magnets attached to the rails. This repulsive force levitates the platform, preventing it from rubbing or grinding against any surfaces. As a result, the platform floats in midair, free from mechanical constraints, ready to glide wherever the rotating shaft’s magnetic field directs it.
Independence from external power sources
One of LIRO’s defining features is its lack of continuous electrical power consumption for levitation and movement. Standard linear motors require coils to be energized along their entire track, but LIRO relies entirely on permanent magnets. Once the shaft begins to rotate, the magnets create the traveling wave that moves the platform. This makes LIRO ideal for remote locations, explosive atmospheres where electrical sparks are a concern, or any scenario where external power is either scarce or undesirable.
System advantages
- No ongoing electricity for levitation
Without relying on electromagnetic coils, LIRO significantly reduces operating expenses and eliminates the risk of electrical faults. - Efficient, precise motion
With minimal friction and no mechanical contact, the system provides smooth, accurate movement, cutting maintenance needs. - Lower costs
A simpler design and the absence of complex coil arrays or constant power input mean manufacturing and upkeep are generally less expensive than more elaborate maglev systems.
Applications across industries
- Artificial lifting: LIRO can raise water, oil, or other fluids from deep wells without the need for electric pumps, thereby lowering energy consumption and reducing mechanical wear.
- Elevators: By adopting permanent magnets and a rotating shaft, buildings can install lift systems that offer smooth, quiet rides, unhampered by traditional cable or hydraulic constraints.
- Goods transport: Whether shifting crates in a warehouse or moving components in a factory, LIRO provides horizontal or vertical transport without friction or sparks.
- Other specialized uses: From handling fragile items like glass or microchips to operating in explosive or remote environments, LIRO’s minimal-power, contact-free design expands its potential in ways traditional motors cannot match.
In essence, LIRO merges the principles of a linear motor with the reliability of permanent magnets. By eliminating continuous electrical coils and mechanical friction, it stands as a versatile, easy-to-maintain solution for everything from high-rise elevators to remote pumping systems.